Printed Circuit Boards (PCBs) are the main element of most modern electronic devices, providing a base for connecting various electronic components.
Understanding PCBs is required for anyone involved in electronics, from engineers to hobbyists.
This guide will walk you through ten essential facts about PCBs, covering their history, structure, types, materials, manufacturing, design software, prototyping, applications, quality standards, and future trends.
By the end, you’ll have a thorough understanding of these components and their role in advancing technology.
Read on to discover everything you need to know about PCB types, and why they are indispensable in today’s tech-driven society.
1. History of PCBs
The history of PCBs dates back to the early 20th century. Invented by Paul Eisler in 1936, PCBs revolutionised electronics by providing a compact, reliable means of connecting components.
Initially used in military applications during World War II, their adoption quickly spread to consumer electronics in the 1950s.
Key milestones in PCB changes include the introduction of multi-layer boards in the 1960s and the development of surface-mount technology in the 1980s.
Companies like IBM and Apple played significant roles in advancing PCB technology.
Today, PCBs are essential in virtually all electronic devices, from smartphones to sophisticated medical equipment, highlighting their impact on the industry.
2. Basic Structure of a PCB
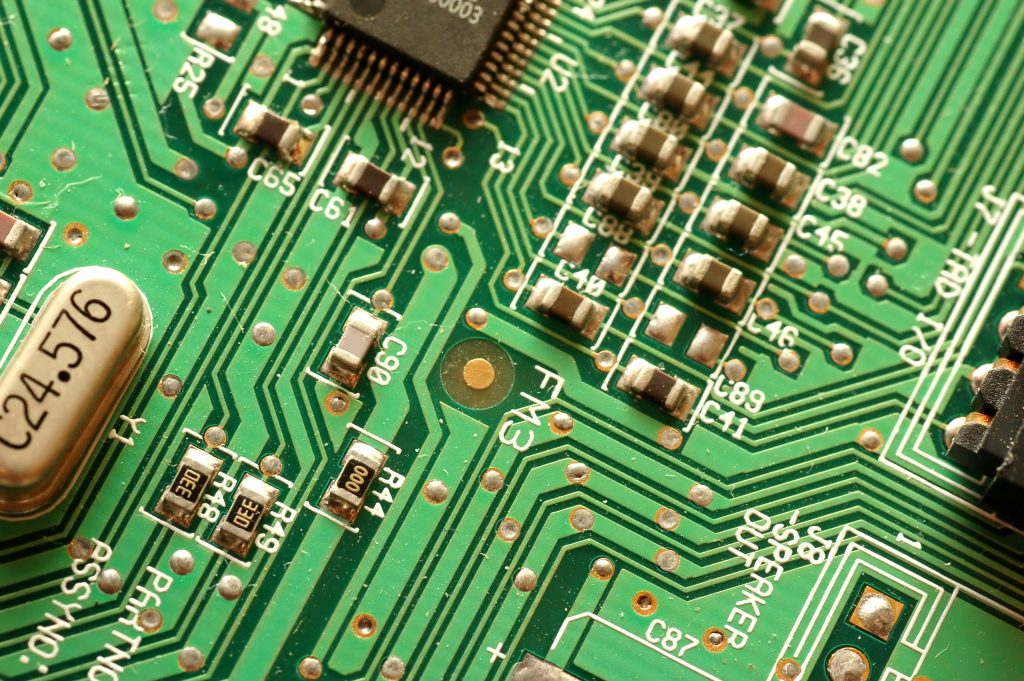
A PCB is a complex yet essential component in electronics, and understanding its structure is strongly advised.
One of the main PCB facts is that its basic structure comprises several layers, each serving a specific function.
At the core is the substrate, typically made from PCB materials like FR4, a type of fibreglass known for its durability and insulation properties.
This core layer is followed by a thin copper layer that forms the electrical pathways.
Above the copper layer is the solder mask, which prevents short circuits by insulating the copper traces.
Finally, the silkscreen layer is applied, displaying labels and markers for easier component placement.
These layers work together to assist the PCB’s functionality and reliability, making it an integral part of modern electronics.
3. Types of PCBs
PCBs come in various types, each designed for specific applications.
Single-sided PCBs are used in simple electronics, while double-sided PCBs offer more complexity.
Multi-layer PCBs, with multiple substrate layers, are used in advanced electronics.
Rigid PCBs are found in devices like computers, flexible PCBs in wearable tech, and rigid-flex PCBs provide both durability and flexibility.
Understanding these types helps in selecting the right PCB, considering the PCB manufacturing process and design software capabilities.
4. Materials Used in PCBs
The performance and reliability of PCBs are greatly influenced by their materials. Common materials include FR4, polyimide, and metal cores.
FR4, a fibreglass and epoxy resin mix, is valued for its insulation and durability, making it a staple in general electronics.
Polyimide offers flexibility and thermal stability, ideal for flexible PCBs in wearables and aerospace.
Metal cores, like aluminium or copper, are essential for high-power applications requiring efficient heat dissipation.
Innovations in these materials drive advancements in PCB manufacturing.
5. PCB Manufacturing Process
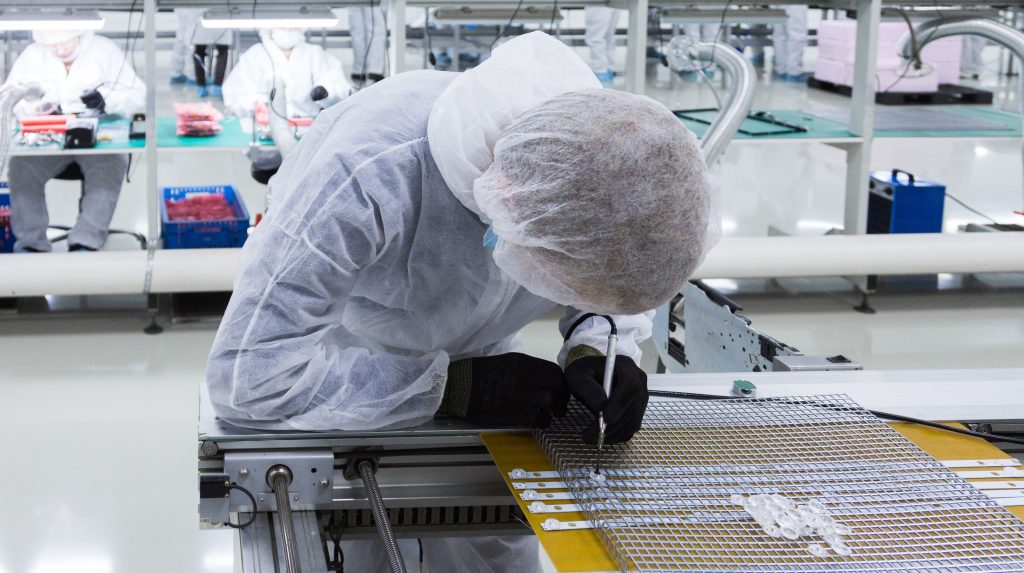
The PCB manufacturing process involves several steps to achieve quality and functionality.
It begins with the design phase, where engineers use PCB design software like Eagle, Altium Designer, or KiCad to create detailed schematics.
Once the design is finalised, it’s printed onto the substrate using various methods, including silk screening and direct imaging.
Next, the board undergoes etching to remove excess copper, leaving only the desired circuit traces.
Layering involves adding additional copper and insulating layers for multi-layer PCBs.
Drilling creates holes for component leads and vias, which are then plated to allow for electrical connectivity.
The board is then soldered, where components are attached to the PCB.
Each stage of the PCB manufacturing process is required for the board’s reliability and performance, and this helps towards the overall PCB layout.
For detailed guidance, you can explore our blog on PCB layout and our page on PCB assembly.
6. Common PCB Design Software
Choosing the right PCB design software is essential for creating efficient circuit boards.
Popular options include Eagle, Altium Designer, KiCad, and OrCAD.
Eagle is user-friendly and ideal for beginners and professionals. Altium Designer offers advanced features for complex projects.
KiCad is a powerful, open-source choice for hobbyists and small businesses.
OrCAD excels in simulation and integration for industrial applications. Each software caters to specific needs, improving the PCB manufacturing process.
7. Importance of PCB Prototyping
PCB prototyping is a major step in the development of any electronic device.
It allows engineers to test and validate their designs before full-scale production, identifying and addressing potential issues early on.
Creating prototypes helps in refining the PCB layout, meaning that all components work together without any issues.
Prototyping also offers significant cost-saving benefits by reducing the likelihood of errors in the final product.
Common prototyping methods include breadboarding, 3D printing, and using small-run PCB manufacturing services.
These methods provide valuable insights and enable iterative improvements.
Successful prototyping can lead to improved performance, reliability, and customer satisfaction.
For example, many tech companies have successfully reduced time-to-market and improved product quality through thorough prototyping.
Introducing a prototyping phase is essential for achieving a high-quality end product.
8. Applications of PCBs
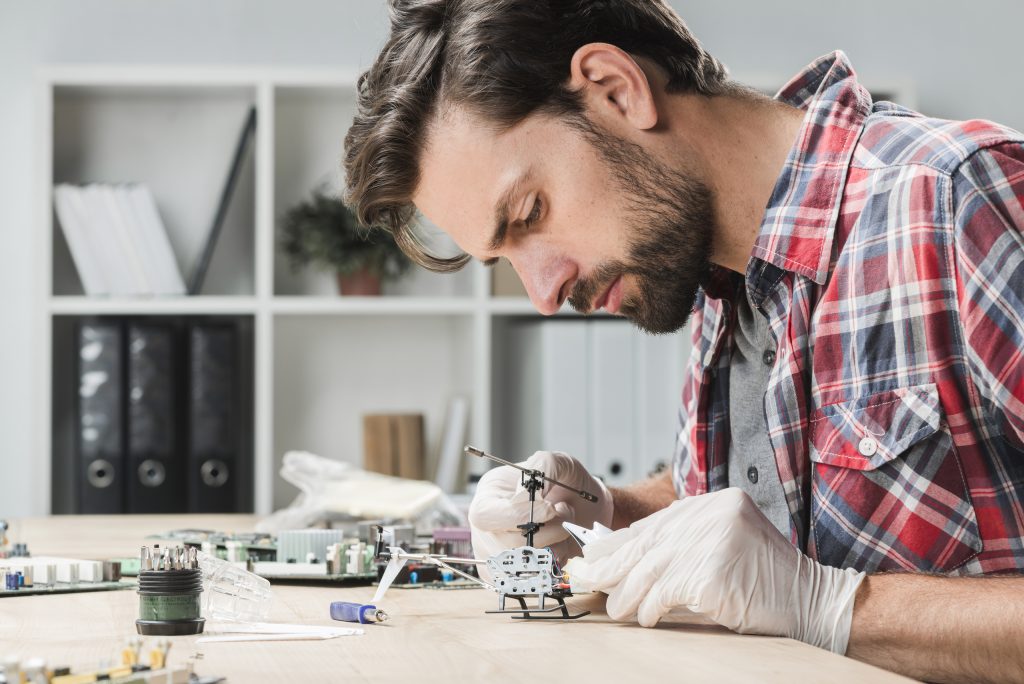
PCBs are essential across various industries. In consumer electronics, they’re found in smartphones, tablets, and laptops.
Automotive systems rely on PCBs for navigation, control, and safety. Medical devices, including MRI machines and pacemakers, also depend on them.
Aerospace applications use PCBs for navigation and communication. Additionally, PCBs are vital in industrial equipment, enabling automation and control.
Emerging technologies like IoT and wearable tech further highlight their versatility.
9. PCB Quality Standards
Making sure there is quality and reliability when it comes to PCBs is required, and this is achieved through adherence to established quality standards.
Key standards include those set by the Association Connecting Electronics Industries (IPC), which provides comprehensive guidelines on PCB design, manufacture, and testing.
IPC standards cover various aspects such as material selection, component placement, and soldering techniques.
International Organisation for Standardisation (ISO) certifications, such as ISO 9001, make sure that PCB manufacturers maintain consistent quality management practices.
Underwriters Laboratories (UL) certification is also needed for safety and compliance, particularly in products requiring electrical safety assurances.
Adhering to these standards guarantees that PCBs meet rigorous performance and safety criteria, reducing the risk of failures and improving the overall product reliability.
Following quality standards is essential for maintaining customer trust and satisfaction in the competitive electronics market.
10. Future Trends in PCB Technology
The future of PCBs is set for significant advancements due to emerging technologies and industry needs.
Key trends include developing flexible and stretchable PCBs for wearable tech and flexible displays, increasing IoT integration for smarter devices, and ongoing miniaturisation efforts to improve functionality in compact electronics.
Additionally, advancements in materials like graphene are expected to improve PCB performance and durability, highlighting the nature of PCB technology.
PCBs are essential to modern electronics, with a rich history and diverse types. The key to reliable products is understanding their design, manufacturing, prototyping, and quality standards.
Their evolving applications and future trends underscore the need to stay informed.
Understanding PCBs is crucial for anyone involved in electronics, whether you are an engineer, student, or tech enthusiast. Throughout this guide, we have explored ten essential facts about PCBs, covering their history, structure, types, materials, manufacturing processes, design software, prototyping importance, diverse applications, quality standards, and future trends.
To recap:
- PCBs have a rich history that has significantly impacted modern electronics.
- The basic structure of PCBs is fundamental to their functionality.
- Various types of PCBs cater to different applications and requirements.
- Materials used in PCBs influence their performance and reliability.
- The manufacturing process is intricate and vital for quality assurance.
- Design software is critical for creating efficient PCB layouts.
- Prototyping helps validate designs and improve final products.
- Applications of PCBs are vast, spanning multiple industries.
- Quality standards ensure the reliability and safety of PCBs.
- Future trends will continue to evolve and enhance PCB technology.
By understanding these aspects, you can appreciate the complexity and importance of PCBs in advancing technology. Staying informed about these key points will not only enhance your knowledge but also help you make informed decisions in your projects and career.
For more detailed information or any inquiries, feel free to contact us.