Printed Circuit Boards (PCBs) come in various types, each designed for specific applications and performance requirements.
Understanding the different types of PCBs is required for anyone involved in electronics, from enthusiasts and students to professionals and engineers.
This article aims to shed light on five key types of PCBs: single-sided, double-sided, multilayer, rigid, and flexible PCBs, explaining their unique features, applications, and advantages.
PCB assembly is a complex process that requires expertise and precision.
1. Single-Sided PCBs
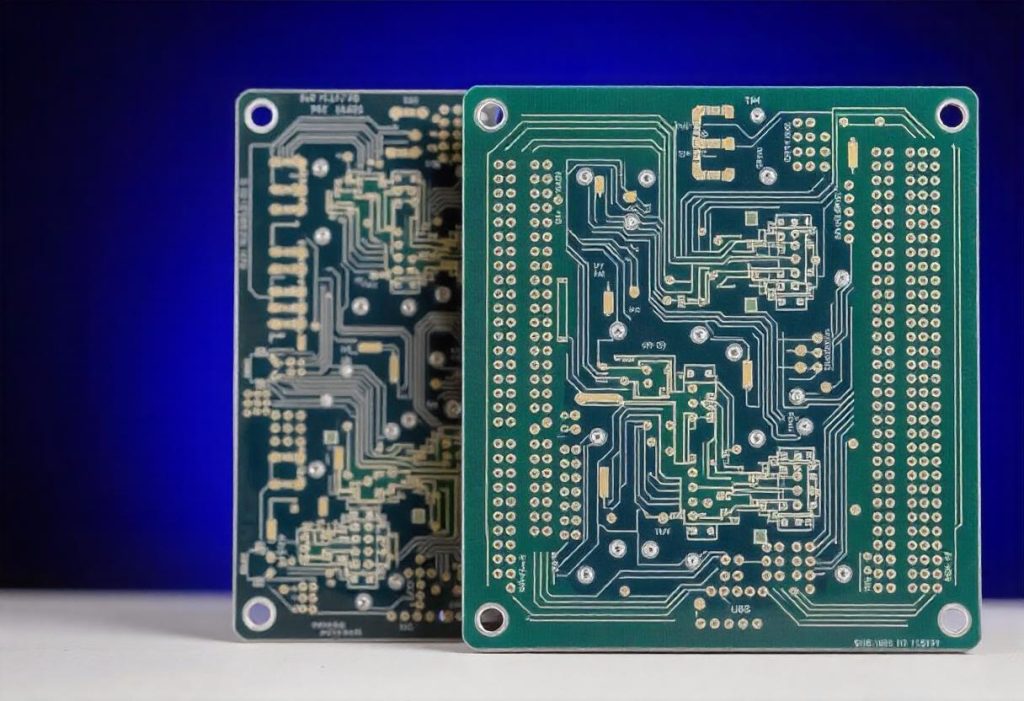
Single-sided PCBs are the simplest type, featuring a single layer of conductive material on one side of the board.
Typically made from materials like FR4 (fibreglass), phenolic, or epoxy, these boards are used in low-density applications.
Single-sided PCBs are commonly found in consumer electronics, such as calculators, radios, and LED lights.
They are ideal for simple devices that do not require complex circuitry.
The main advantage of single-sided PCBs is their low cost and ease of manufacture.
However, their limited circuitry space and lower performance capabilities make them unsuitable for more complex applications.
The manufacturing process of single-sided PCBs involves applying a layer of copper to one side of the board, followed by a protective solder mask to prevent oxidation.
Components are then mounted and soldered to the copper traces.
This straightforward design makes single-sided PCBs cost-effective and easy to produce in large quantities, making them a popular choice for basic electronic products.
2. Double-sided PCBs
Double-sided PCBs have conductive material on both sides of the board, allowing for more complex circuitry and component placement.
This design includes vias (small holes) that connect the circuits on each side.
While single-sided PCBs are simpler, double-sided PCBs offer more flexibility and higher performance due to their increased surface area for components.
Double-sided PCBs are used in a variety of applications, including industrial controls, power supplies, and instrumentation.
These PCBs provide better circuit density and are more cost-effective than multilayer PCBs.
However, they can be more challenging to design and manufacture due to the need for precise alignment and through-hole connections.
In double-sided PCBs, components can be placed on both sides of the board, which allows for a more compact and efficient design.
The use of vias to connect circuits on both sides enables more intricate designs, making them suitable for complex devices such as amplifiers, HVAC systems, and automotive electronics.
Despite their complexity, double-sided PCBs strike a balance between performance and cost, making them a versatile choice for many applications.
3. Multilayer PCBs
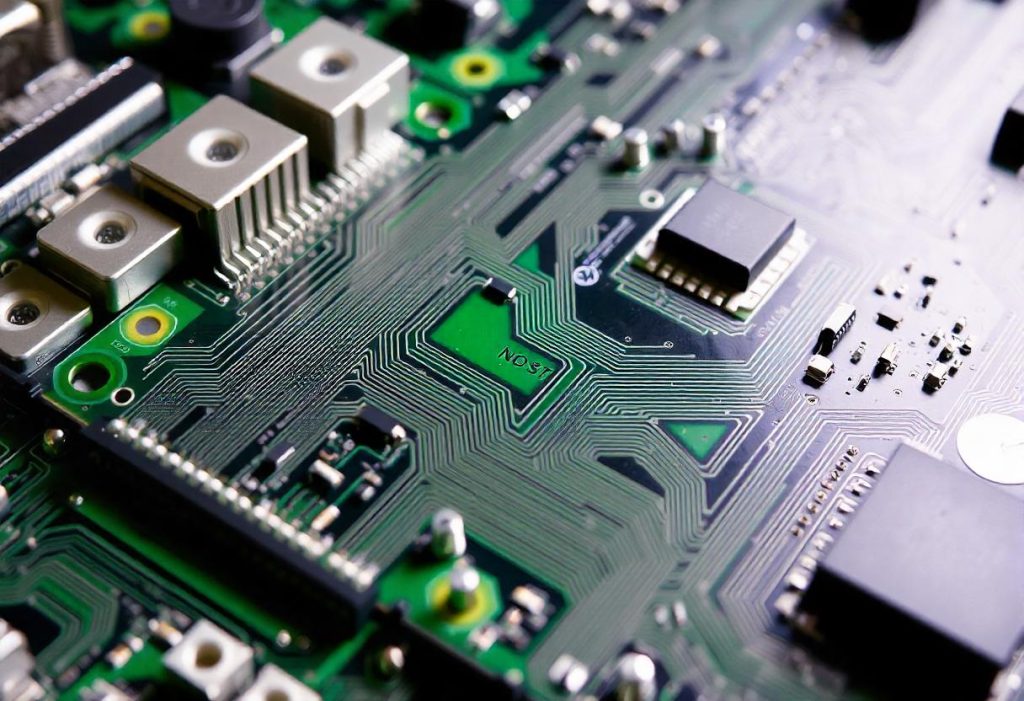
Multilayer PCBs consist of multiple layers of conductive material separated by insulating layers.
This structure allows for highly complex and compact circuit designs, making them suitable for advanced electronics.
Multilayer PCBs can have three or more layers, with each layer serving different functions.
The layers are laminated together under high pressure and temperature to create a single, cohesive board.
The design and manufacturing of multilayer PCBs are intricate processes, requiring advanced techniques to allow for proper layer alignment and electrical connections.
These PCBs are commonly used in high-performance devices such as computers, smartphones, and medical equipment.
While multilayer PCBs offer superior performance and functionality, they are also more expensive and complex to produce compared to single or double-sided PCBs.
Multilayer PCBs are ideal for applications that demand high-speed processing and large data-handling capabilities.
Their complex design allows for greater functionality in a smaller footprint, making them essential for modern electronics.
The ability to include multiple power and ground planes within the layers helps to reduce electromagnetic interference and improve signal integrity.
As a result, multilayer PCBs are used in sophisticated equipment like aerospace systems, advanced communication devices, and cutting-edge medical instruments.
4. Rigid PCBs
Rigid PCBs are made from solid, inflexible materials that provide structural support for the components mounted on them.
They are known for their durability and reliability. Rigid PCBs are typically made from materials like FR4 or metal cores, which provide excellent mechanical strength and stability.
Common materials include fibreglass, copper, and aluminium, chosen for their robustness and conductivity.
Rigid PCBs are used in a wide range of devices, including desktop computers, televisions, and industrial machinery.
The main advantages of rigid PCBs are their stability and durability.
However, their lack of flexibility makes them unsuitable for applications where bending or movement is required.
The manufacturing process of rigid PCBs involves layering copper on a rigid substrate, followed by a solder mask and silkscreen printing for component placement.
This construction provides a sturdy and reliable platform for electronic components, allowing for consistent performance in demanding environments.
Rigid PCBs are essential in devices that require a solid foundation and reliable electrical connections, such as computer motherboards, power supplies, and automotive control systems.
5. Flexible PCBs
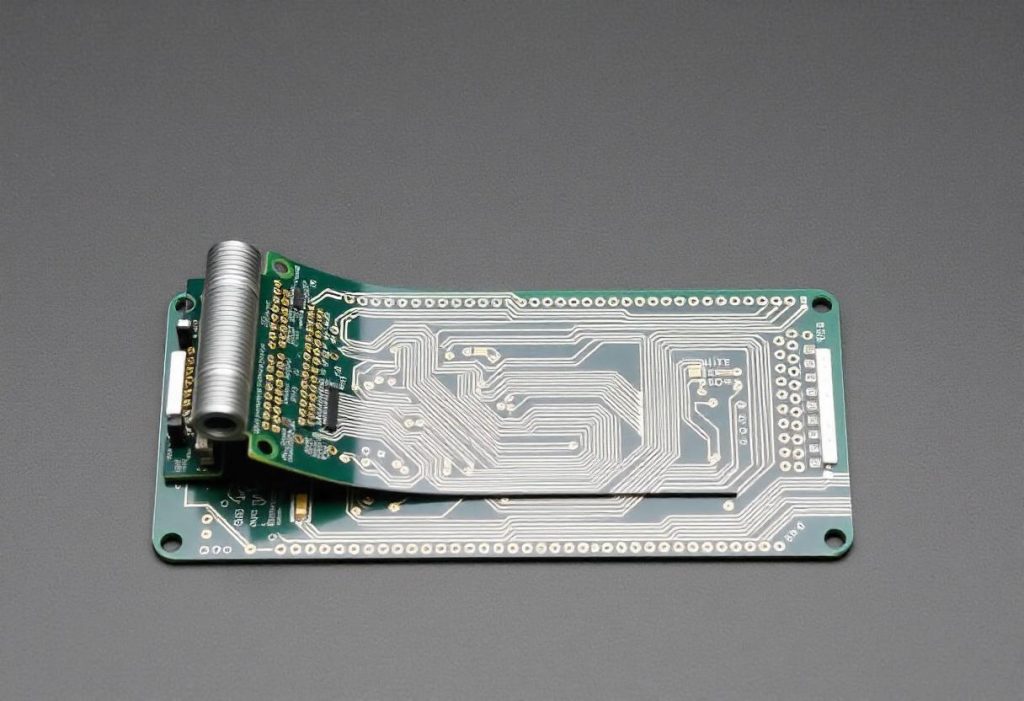
Flexible PCBs, or flex PCBs, are designed to bend and flex without breaking, making them ideal for dynamic applications where space and movement are considerations.
These PCBs are made from flexible plastic substrates like polyimide, which can withstand bending and twisting.
Flex PCBs require special design considerations so they can handle the mechanical stress of flexing.
They are often used in conjunction with rigid PCBs in a hybrid design.
Flex PCBs are used in a variety of applications, including wearable devices, flexible displays, and medical equipment.
The primary strength of flexible PCBs is their ability to fit into tight spaces and move without breaking.
However, they can be more expensive to produce and may require more complex assembly processes compared to rigid PCBs.
The fabrication of flexible PCBs involves using thin, flexible materials that can be folded or twisted as needed.
This flexibility allows for innovative designs in compact devices where traditional rigid PCBs would not fit.
Flexible PCBs are commonly used in applications that require frequent bending or dynamic movement, such as in robotics, portable electronics, and flexible solar panels.
Despite the higher production cost, the versatility and space-saving benefits of flexible PCBs make them an invaluable component in modern electronic design.
In summary, understanding the different types of PCBs is key for selecting the right one to meet your specific needs.
Each type offers distinct advantages and caters to various applications, ensuring optimal performance for different electronic projects. As PCB technology continues to evolve, staying updated with the latest trends and advancements is essential.
For more detailed information or to discuss how Altimex can support your PCB requirements, please contact us.