Printed Circuit Boards (PCBs) are essential to modern electronics, serving as the base for many devices that operate. As technology continues to advance, the complexity of PCB designs has also increased, presenting a range of challenges for designers and manufacturers alike. Understanding and addressing these challenges early in the design phase is useful for achieving peak functionality and reliability in electronic products.
This article will discuss six common PCB challenges in terms of design, from signal integrity issues to thermal management problems, and provide practical solutions for each. By tackling these issues proactively, PCB designers can significantly improve the performance and manufacturability of their products, ultimately leading to more efficient and reliable electronic systems.
1. Signal Integrity Issues and Solutions
Signal integrity refers to the quality of electrical signals within a PCB, and it is essential for the reliable performance of electronic devices. Poor signal integrity can lead to data corruption, increased errors, and ultimately, device malfunction. Common causes of signal integrity problems include impedance mismatch, cross-talk between traces, and inadequate grounding.
To address these issues, designers can adopt several best practices. First, proper routing techniques, such as maintaining consistent trace widths and lengths, help to preserve signal integrity. Additionally, using controlled impedance for signal traces can prevent reflections and improve overall performance.
Simulation tools play a major role in assessing signal integrity before production. By conducting thorough simulations, designers can identify potential problems and implement solutions early in the design process, ultimately reducing costly revisions and delays in manufacturing.
2. Thermal Management Problems and Solutions
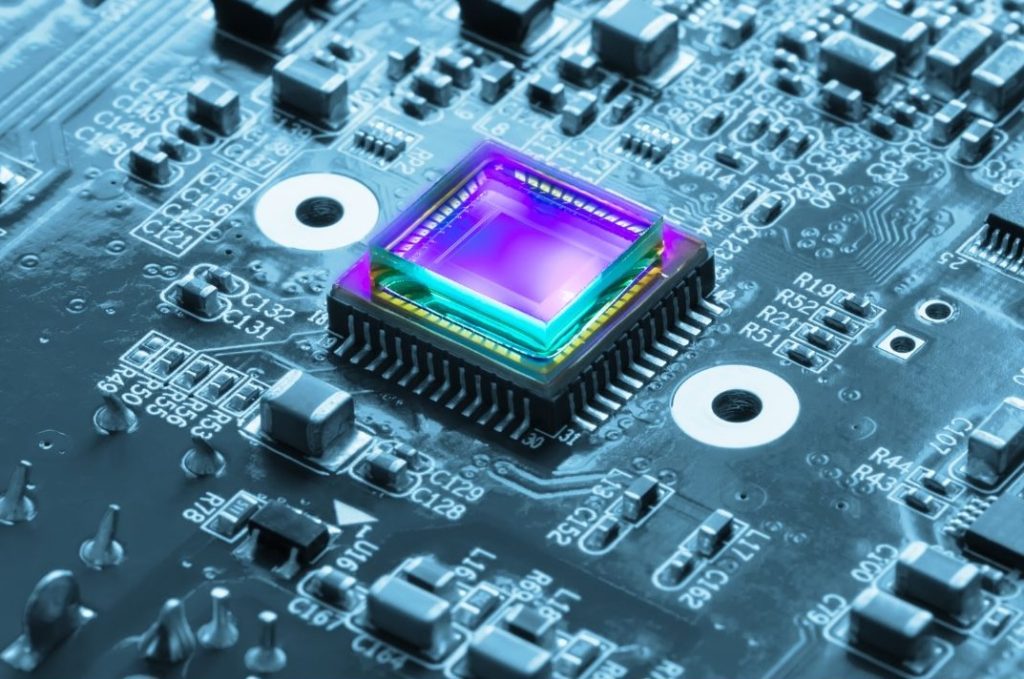
Effective thermal management is needed for the performance and longevity of PCBs. Excessive heat can lead to reduced reliability, shortened lifespan, and even complete failure of electronic components. Common sources of thermal issues include high-power components, dense layouts, and insufficient heat dissipation measures.
To address these challenges, designers can implement several strategies. Using thermal vias, heat sinks, and thermal pads can help dissipate heat effectively, allowing components to operate within their safe temperature ranges. Additionally, proper placement of components on the PCB can improve airflow and promote better thermal management.
Software tools are also available for thermal analysis, allowing designers to simulate heat distribution and identify potential problem areas before production. By tackling thermal management concerns early, designers can create more reliable and efficient PCB designs that withstand the demands of modern electronics.
3. Component Placement Constraints and Solutions
Component placement is a significant aspect of PCB design that directly affects performance, manufacturability, and overall functionality. In compact designs, managing space and achieving the most useful component placement can be particularly challenging. Poor placement can lead to signal integrity issues, heat concentration, and increased electromagnetic interference.
To address these constraints, designers should follow guidelines for optimal placement. Components should be arranged to facilitate signal flow and heat distribution while minimising interference. For high-density designs, using smaller components and multi-layer boards can help maximise available space.
Collaboration with manufacturing teams is essential to confirm that component placement is practical and aligns with assembly processes. Early communication can help identify potential placement issues, allowing designers to make adjustments before finalising their designs. This proactive approach leads to smoother manufacturing and improved overall PCB performance.
4. Electromagnetic Interference (EMI) Challenges and Solutions
Electromagnetic interference (EMI) can significantly affect the performance of PCBs, leading to malfunctions and degraded functionality. EMI arises from various sources, including high-speed signals, power supplies, and external electromagnetic fields. It can disrupt the signals on a PCB, resulting in data errors and reduced performance.
To address EMI, designers can implement several effective strategies. Proper grounding techniques are essential; having all components share a common ground can reduce the effects of EMI. Additionally, shielding techniques, such as enclosing sensitive components within conductive enclosures, can help block external interference.
Using ferrite beads on signal lines can also help suppress high-frequency noise, further reducing EMI susceptibility. Designing PCBs with these considerations in mind will improve resilience against electromagnetic interference, leading to more reliable and efficient electronic devices.
5. Manufacturing Defects and Solutions
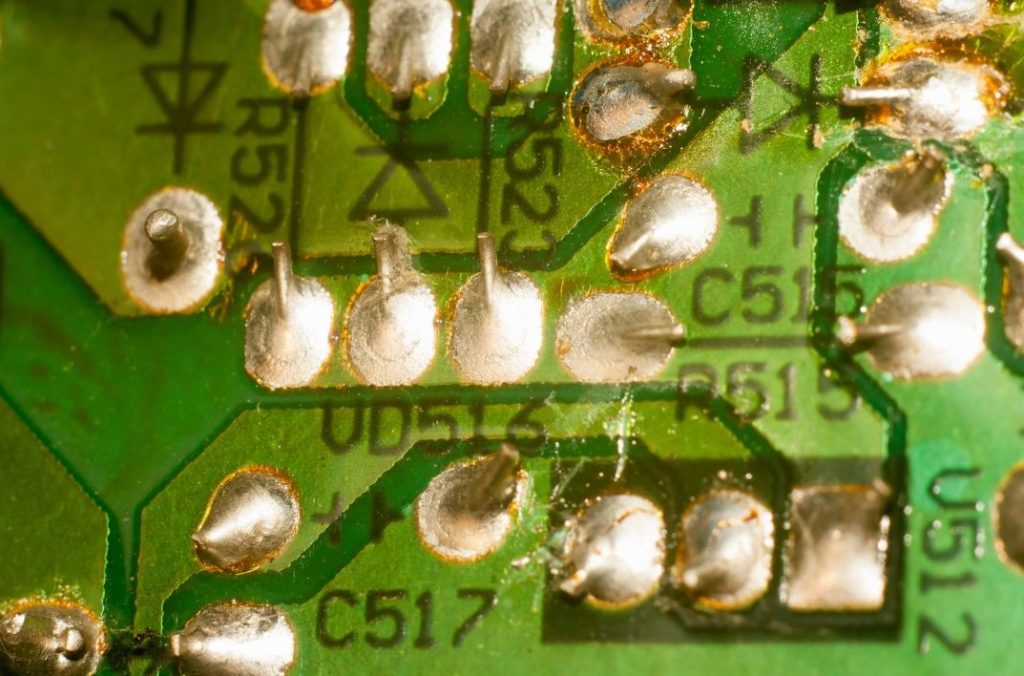
Manufacturing defects are a significant concern in PCB production and can lead to costly delays and product failures. Common defects include shorts, opens, and solder bridging, which can arise from various factors such as design flaws, material issues, and improper manufacturing processes.
To minimise defects, designers should adopt Design for Manufacturability (DFM) principles. These principles encourage the creation of designs that are easier and more cost-effective to manufacture, including considerations like trace widths, pad sizes, and spacing between components.
Prototyping and testing are also essential steps in the design process. By creating prototypes and conducting thorough testing, designers can identify and rectify defects early, reducing the likelihood of issues during mass production. Early detection of manufacturing defects leads to more reliable PCBs and improves overall product quality.
6. Limited Board Space and Solutions
Limited board space is a common challenge in modern PCB designs, particularly as electronic devices become smaller and more compact. This constraint can impact performance, functionality, and manufacturability. Designers often face the dilemma of fitting more components into a limited area without compromising quality or performance.
To address these challenges, various techniques can be employed. Using multi-layer boards allows designers to maximise space by stacking multiple layers of circuitry. This approach enables the integration of more components in a smaller footprint. Additionally, utilising miniaturised components can help free up valuable space on the board.
Designers should prioritise the placement of components based on functionality and signal flow to optimise available space. Several software tools can assist in this process, providing simulations and layout options that facilitate effective design within space constraints. By strategically addressing space limitations, designers can create efficient and high-performing PCBs.
Understanding the common challenges of a PCB design is essential for creating reliable and efficient electronic systems. This article has outlined six significant challenges: signal integrity issues, thermal management problems, component placement constraints, electromagnetic interference, manufacturing defects, and limited board space. Each of these challenges requires careful consideration and proactive measures to address effectively.
By implementing best practices and leveraging available tools and techniques, designers can improve the performance and manufacturability of their PCBs.
This not only improves the functionality of the end products but also contributes to overall quality and reliability. Continuous learning and adaptation to new technologies will further empower PCB designers to tackle emerging challenges in electronics.