A backplane PCB serves as a central connector in electronic systems, linking multiple circuit boards to allow efficient communication and power sharing. It is widely used in high-performance servers, telecom equipment, and industrial control systems, supporting data transmission and power distribution. Backplane PCBs provide a way to manage connections between different components, minimising the need for extensive cabling and helping to improve system reliability by reducing the potential for mechanical failure.
The need for backplane PCBs has grown as electronic systems become more complex, especially in industries that require high-speed data transfer and robust power management. From telecommunications to automotive and aerospace, backplane PCBs are essential so that modern systems can handle the increasing demands of data processing and energy efficiency.
In this guide, we will cover the different types of backplane PCBs, their components, useful design considerations, and the manufacturing processes involved in creating them. Understanding these aspects is useful for making informed decisions when designing or selecting backplane PCBs for complex electronic systems.
What is a Backplane PCB?
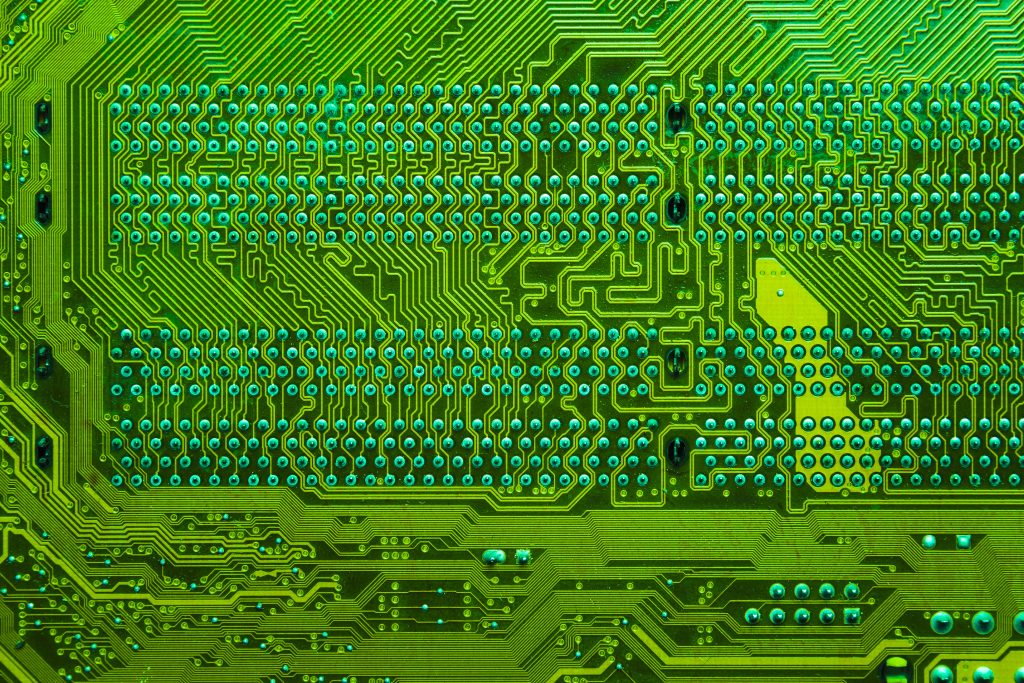
A backplane PCB is designed to connect multiple printed circuit boards (PCBs) within an electronic system, allowing data and power to flow between them. By simplifying the connections, it helps to manage complex wiring and supports the distribution of signals and power across various components.
A backplane PCB reduces the need for numerous cables or wiring harnesses, making the overall system design more manageable, particularly in large-scale applications. This is especially relevant in industries where space is at a premium and where wiring complexity can lead to inefficiencies and maintenance challenges.
Role in Electronics
Backplanes are often found in applications where high-speed data transfer and reliable power management are essential, such as servers, telecommunications equipment, and industrial systems. In data centres, for example, backplane PCBs are needed to enable the rapid transmission of vast amounts of information across multiple servers and devices. In aerospace, where reliability and durability are key, backplane PCBs help so that various avionics systems can communicate effectively under extreme conditions.
Basic Functionality
By reducing the complexity of wiring, backplane PCBs also make it easier to maintain modular systems, where different circuit boards can be swapped or replaced without the need to redesign the entire system. This modularity is particularly useful in industries that require regular upgrades or where equipment needs to be serviced frequently. Backplane PCBs support signal routing and power delivery, helping to maintain efficiency in systems that require quick data transfer and smooth operation. Industries that rely on backplane PCBs include data centres, aerospace, automotive, medical equipment, and industrial automation, where the ability to manage multiple components is fundamental to system performance.
Types of Backplane PCBs
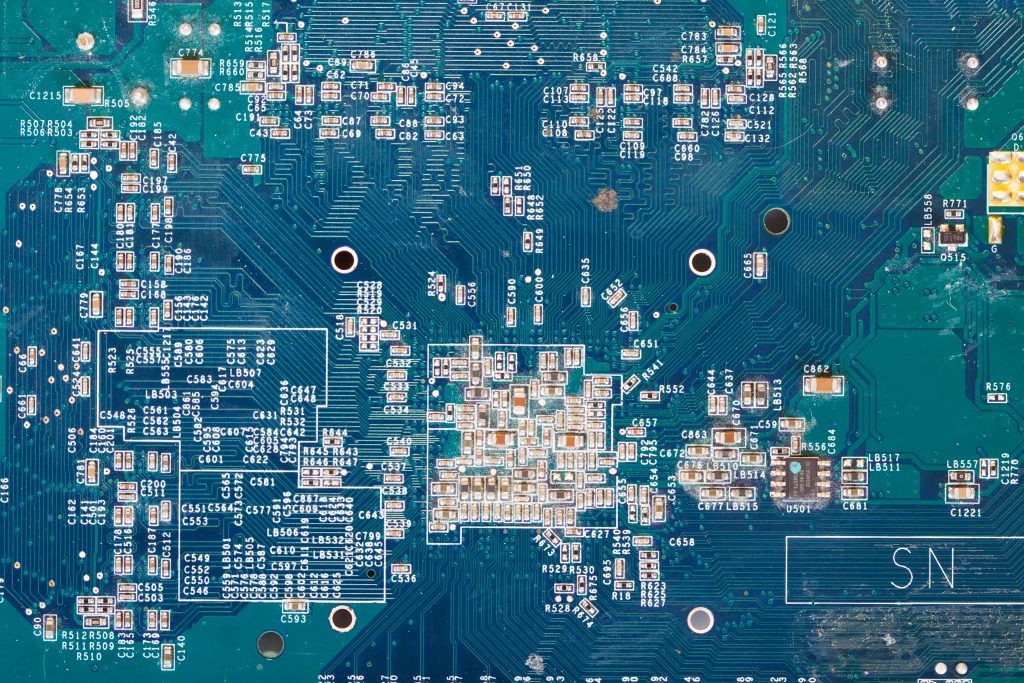
Backplane PCBs come in various types, each designed to meet different operational requirements. Understanding these types is important for selecting the right backplane for specific applications. Each type of backplane PCB offers unique advantages and trade-offs, depending on the specific needs of the system in which it is used.
Active
An active backplane PCB includes components such as chips or integrated circuits (ICs) to manage signals. This type processes signals passing through it, making it suitable for systems that require specific control over data transmission. Active backplanes are often used in high-performance computing systems where maintaining signal quality is a key consideration, improving data flow within complex electronic setups. Active backplanes are particularly useful in environments where signal strength and integrity need to be actively managed to prevent degradation over long distances or in systems with high levels of electromagnetic interference (EMI).
The additional processing capability provided by active components allows for greater flexibility in managing different signal types, meaning that the backplane can handle a wide range of data rates and power requirements. Active backplanes are commonly used in telecommunications, data centres, and high-end industrial systems, where the ability to control and manipulate signals at the Backplane level can significantly improve overall system performance. Despite the added complexity and cost, active backplanes are favoured in situations where signal integrity and data accuracy are required.
Passive
A passive backplane PCB does not include any components for signal processing. It simply serves as a connecting board, allowing signals to pass through without modification. Passive backplanes are generally more cost-effective and are used in systems where signal processing is not needed. These are often found in control systems and other straightforward applications where simplicity is preferred. Passive backplanes are ideal for environments where the system requirements are relatively static, and there is no need for additional signal manipulation at the Backplane level.
The simplicity of passive backplanes also means they are easier to manufacture and maintain, making them an attractive option for cost-conscious projects. They are widely used in simpler control systems, instrumentation, and basic computing setups where the data transfer requirements are more predictable. In systems where the integrity of the signal is not at risk due to environmental factors or the distances involved, passive backplanes offer a reliable and low-cost solution.
Parallel
Parallel backplanes connect components using parallel data lines, which allow for high-speed data transfers. They are well-suited for tasks that require large volumes of data to be moved quickly, such as in telecommunications systems.
Parallel backplanes are designed to handle large amounts of data by simultaneously transmitting multiple bits of data over different lines. However, parallel backplanes can experience signal degradation over longer distances, which may limit their effectiveness in certain setups.
The challenge with parallel backplanes is that, as data speeds increase, the timing of signals across the various lines becomes more difficult to manage.
Signal skew, where different signals arrive at slightly different times, can result in data corruption or errors.
Despite these challenges, parallel backplanes remain a popular choice for high-throughput systems where speed is a top priority. They are often used in legacy systems or in applications where the distances between components are relatively short, thus minimising the risks associated with signal degradation.
Serial
Serial backplanes serially transmit data, one bit at a time, rather than in parallel. This method supports better signal integrity over longer distances, making serial backplanes ideal for modern data communication and networking systems. They are commonly used in industries such as telecommunications, where long-distance data transfer is a significant requirement. The main advantage of serial backplanes is their ability to maintain signal integrity over greater distances, which is particularly important in applications where the backplane must connect components spread out over a larger physical area.
Serial backplanes are typically used in high-speed data environments, such as those found in fibre-optic networks or other advanced communication systems. They are also preferred in environments where electromagnetic interference (EMI) is a concern, as the serial transmission method is less prone to interference than parallel systems. As technology continues to evolve, serial backplanes are increasingly being adopted in place of parallel systems due to their superior performance in modern high-speed networks.
Custom Backplanes
Custom backplane PCBs are specifically designed to meet the unique requirements of specialised equipment. They are often used in fields such as aerospace, medical technology, and defence, where standard solutions may not meet the performance needs. Custom backplanes are designed from the ground up to fit the exact specifications of the system, taking into account factors such as data rates, power requirements, physical space, and environmental conditions.
Custom designs allow for specific functionality based on the application’s demands. In aerospace, for example, custom backplanes must be designed to withstand extreme temperatures, vibration, and radiation, while in medical technology, backplanes may need to support highly accurate data transmission in life-critical systems.
The ability to customise every aspect of the backplane makes this option ideal for industries where performance, reliability, and durability are non-negotiable. While custom backplanes are more expensive and time-consuming to produce, their benefits in specialised applications make them an essential component in high-end systems.
Key Components of a Backplane PCB
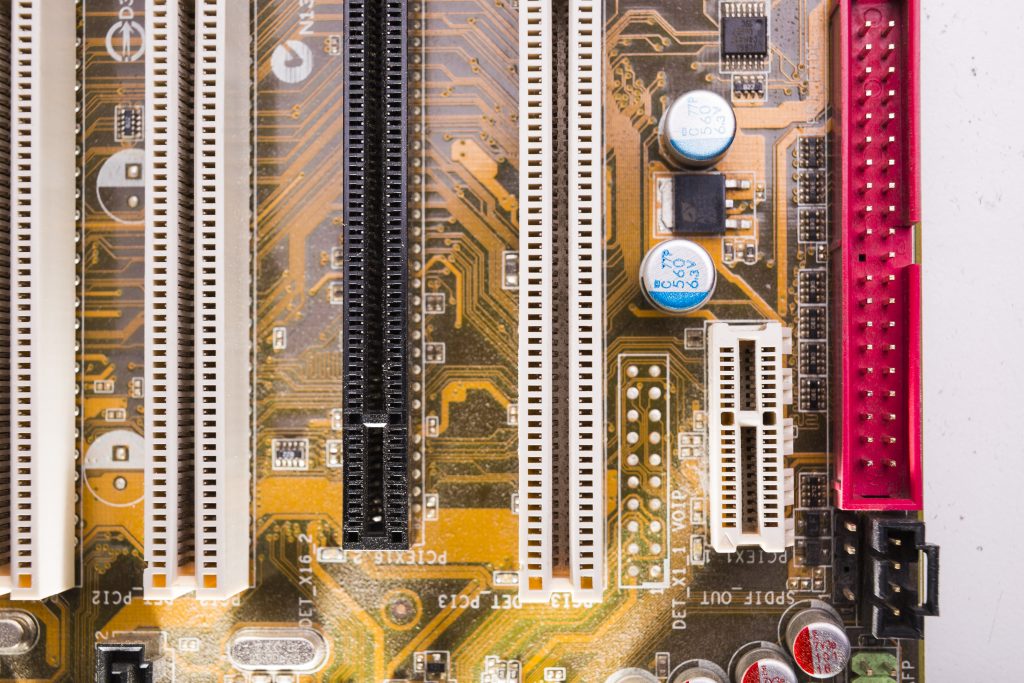
Backplane PCBs consist of several important components that influence their functionality and performance. Understanding these components is essential when designing and selecting the right backplane for different applications.
Connectors
Connectors are a key part of backplane PCBs, providing the interface through which multiple PCBs are linked. These connectors maintain signal quality and allow reliable communication between connected boards. The type and quality of connectors used can significantly affect overall system performance. Common connectors in backplane PCBs include card edge connectors and pin headers, each offering varying levels of durability and compatibility.
Connectors are also needed for determining the system’s ability to handle various signal types, including both analogue and digital signals. High-quality connectors are essential in environments where signal integrity is required, such as in data centres or aerospace systems. The choice of connector material, contact resistance, and the physical layout of the connector can all influence the performance of the backplane, making it necessary to choose the right type for the application.
Power Distribution
Power distribution is another major function of backplane PCBs, as they deliver power across the connected boards. Effective power management supports system stability, particularly in systems with high power requirements. Backplane PCBs are designed to handle different power loads, and features like dedicated power planes help manage power delivery effectively, reducing the risk of surges or imbalances.
In high-performance systems, the backplane must not only distribute power efficiently but also protect against potential power surges or fluctuations. This requires careful planning in the design phase to incorporate features like redundant power lines, fuses, and current protection devices. Systems that rely on backplanes, such as industrial control systems or telecommunications equipment, often have demanding power requirements that must be met consistently for the system to function correctly.
Data Lines
Data lines on a backplane PCB transmit signals between connected components. The design of these data lines plays a significant role in maintaining fast and reliable data communication. Depending on the application, either parallel or serial data lines may be used. Parallel data lines support high-speed transfers but may face signal degradation over long distances, while serial data lines provide better signal quality for long-range transmissions.
Data lines must be carefully designed to minimise interference from other signals or external noise. Shielding, proper grounding, and the use of differential signalling techniques can help improve data transmission quality. For high-speed systems, the layout of data lines must take into account factors such as trace length, impedance matching, and crosstalk to make sure that signals arrive accurately and on time. The choice between parallel and serial data lines often depends on the specific requirements of the system, such as the distance between components and the need for data integrity.
Design Considerations for Backplane PCBs
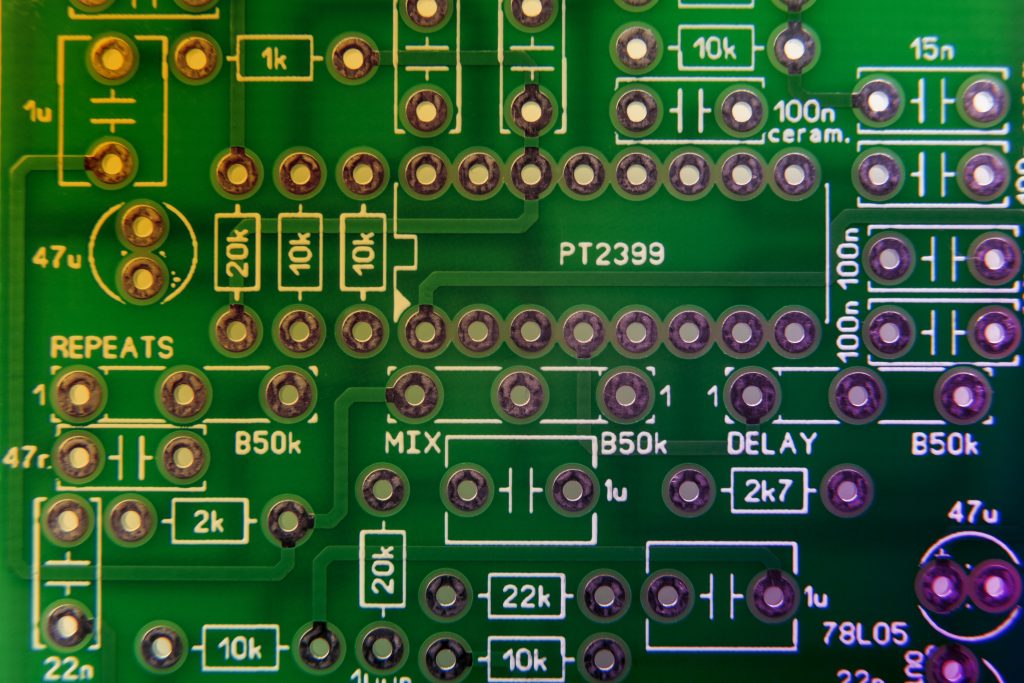
When designing a backplane PCB, several factors must be considered to achieve strong performance and reliability. These design aspects directly affect how well the PCB functions in various applications.
Signal Integrity
Signal integrity refers to the quality of the electrical signals passing through a backplane PCB. Poor signal integrity can result in data errors and reduced system performance. Factors such as trace routing, component placement, and ground planes are useful for maintaining signal quality. Careful design and layout help reduce interference and noise, particularly in systems requiring high-speed data transfers.
In complex systems, signal integrity is influenced by many variables, including trace length, impedance, and the dielectric properties of the PCB material. Proper design practices, such as controlled impedance routing and the use of high-quality connectors, are essential for maintaining signal integrity in backplane PCBs. In applications like telecommunications or high-speed computing, even small variations in signal quality can lead to significant performance issues, making signal integrity one of the top design priorities.
Thermal Management
Thermal management is a major aspect of backplane PCB design. As electronic systems operate, they generate heat, which, if not managed properly, can lead to component failure or reduced efficiency. Methods like heatsinks, improved airflow, and strategic placement of components help dissipate heat effectively. Proper thermal management prolongs the lifespan of the PCB and supports stable operation under high-load conditions.
In high-power applications, such as industrial control systems or data centres, backplane PCBs must be designed to handle significant amounts of heat. This may involve using thermal vias, heat spreaders, or even liquid cooling systems to keep the PCB within safe operating temperatures. The layout of the backplane must be carefully planned to avoid hot spots, and materials with good thermal conductivity may be selected to help manage heat dissipation.
Material Selection
The choice of materials used in a backplane PCB has a direct impact on its performance and durability. Common materials include FR-4, polyimide, and other specialised composites, each offering different levels of heat resistance and signal transmission capabilities. The material chosen must match the application’s specific requirements, such as operating temperature, signal frequency, and environmental conditions. Selecting the right materials helps the PCB meet both performance and durability standards.
Material selection is required when determining the backplane’s ability to handle high-frequency signals and extreme environmental conditions. For example, in aerospace or military applications, the backplane may need to withstand extreme temperatures, vibration, and radiation, requiring the use of advanced materials with superior mechanical and electrical properties. The dielectric constant and loss tangent of the material will affect the signal speed and integrity, making it essential to choose a material that aligns with the system’s performance requirements.
Manufacturing and Testing of Backplane PCBs
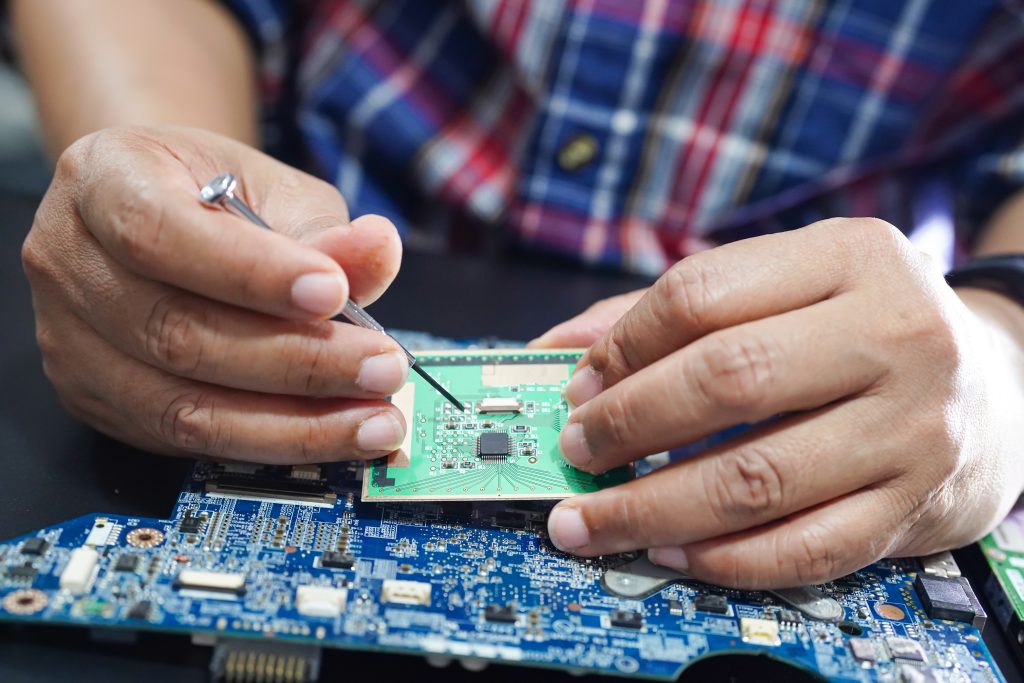
The manufacturing and testing of backplane PCBs require precision and attention to detail. These processes are essential to confirming that the PCB performs reliably and meets the necessary standards for its intended applications.
Fabrication Process
The fabrication of a backplane PCB involves several key stages, including etching, layering, and drilling. One of the biggest factors in manufacturing is confirming that the PCB has the right thickness to support its application. Thicker backplane PCBs may be required for more complex systems, as they often need to support more connections and higher power loads. The precision of the manufacturing process plays a large role in determining the final performance of the Backplane, particularly in terms of signal routing and power distribution.
The choice of materials during fabrication also plays a significant role in the backplane’s ability to perform in different environments. Factors such as the number of layers, copper thickness, and the use of specialised coatings can all influence the overall durability and electrical performance of the PCB. The fabrication process must be closely monitored to make sure that the backplane meets the required specifications, particularly in applications where precision and reliability are needed.
Testing Procedures
After fabrication, backplane PCBs undergo various testing procedures to check for defects and verify performance. Common tests include continuity and impedance testing, which assess the electrical performance of the PCB. These tests help identify any potential issues with signal transmission or power distribution that could affect the overall functionality of the system. Durability testing is also useful to confirm that the Backplane can withstand environmental factors such as temperature fluctuations or mechanical stress.
In addition to electrical testing, mechanical testing may be carried out so that the backplane can withstand physical stress, such as vibrations or impacts. Environmental testing may also be required for backplanes used in harsh environments, such as aerospace or military applications. This can include tests for temperature cycling, humidity, and exposure to corrosive elements. By subjecting the backplane to rigorous testing, manufacturers can make sure that it will perform reliably in its intended application.
Quality Assurance
Quality assurance is an ongoing process throughout the production of a backplane PCB. From the selection of materials to the final inspection, quality checks are carried out at every stage to confirm that the backplane meets industry standards and the specific needs of the application. Certifications and standards, such as ISO and IPC, often apply to backplane PCBs, particularly those used in industries like aerospace or medical technology. Continuous quality control helps minimise the risk of field failures and supports long-term reliability.
In high-reliability applications, such as medical devices or aerospace systems, the backplane must meet stringent quality requirements. This may involve obtaining certifications from third-party organisations to verify that the PCB meets the necessary standards for safety and performance. Ongoing quality checks throughout the production process help to catch any potential issues early, reducing the risk of failures in the field.
Backplane PCBs play a key role in connecting multiple PCBs within a system, supporting both data and power transmission. By understanding the various types, components, and design considerations involved, engineers and designers can select or create backplane PCBs that meet the specific needs of their applications. The manufacturing and testing processes further contribute to the performance and reliability of these systems.
Altimex provides expertise in backplane PCB solutions, offering high-quality products suited to complex electronic systems.